A fluffy sheepskin stays between me and the hard wooden bench at my Glimåkra Standard loom. Softening your loom bench makes weaving that much more pleasant. Last week Jane asked a great question: How do you secure the sheepskin on the bench? To answer that, I invite you to follow along as I secure the sheepskin on my drawloom bench.
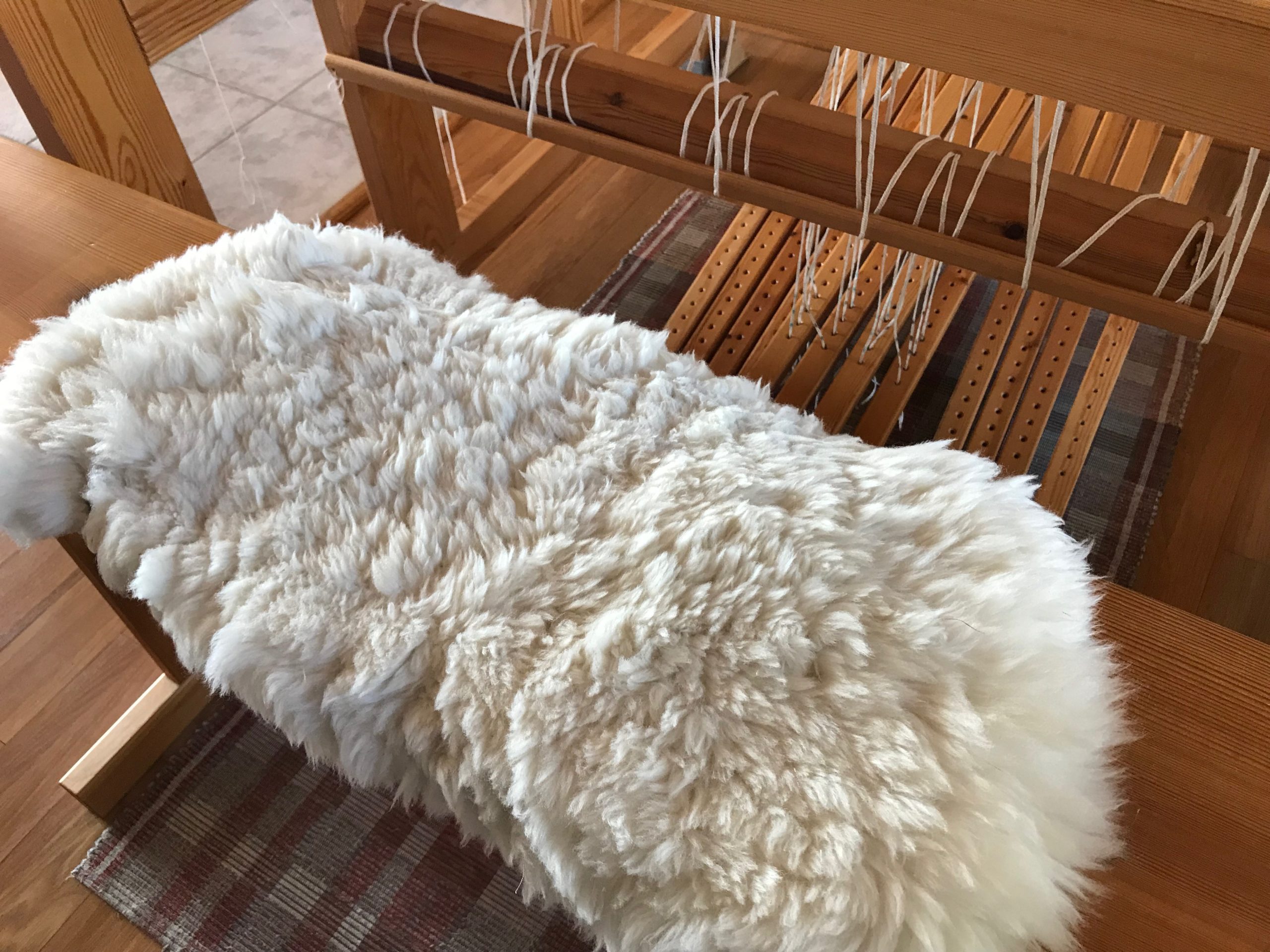
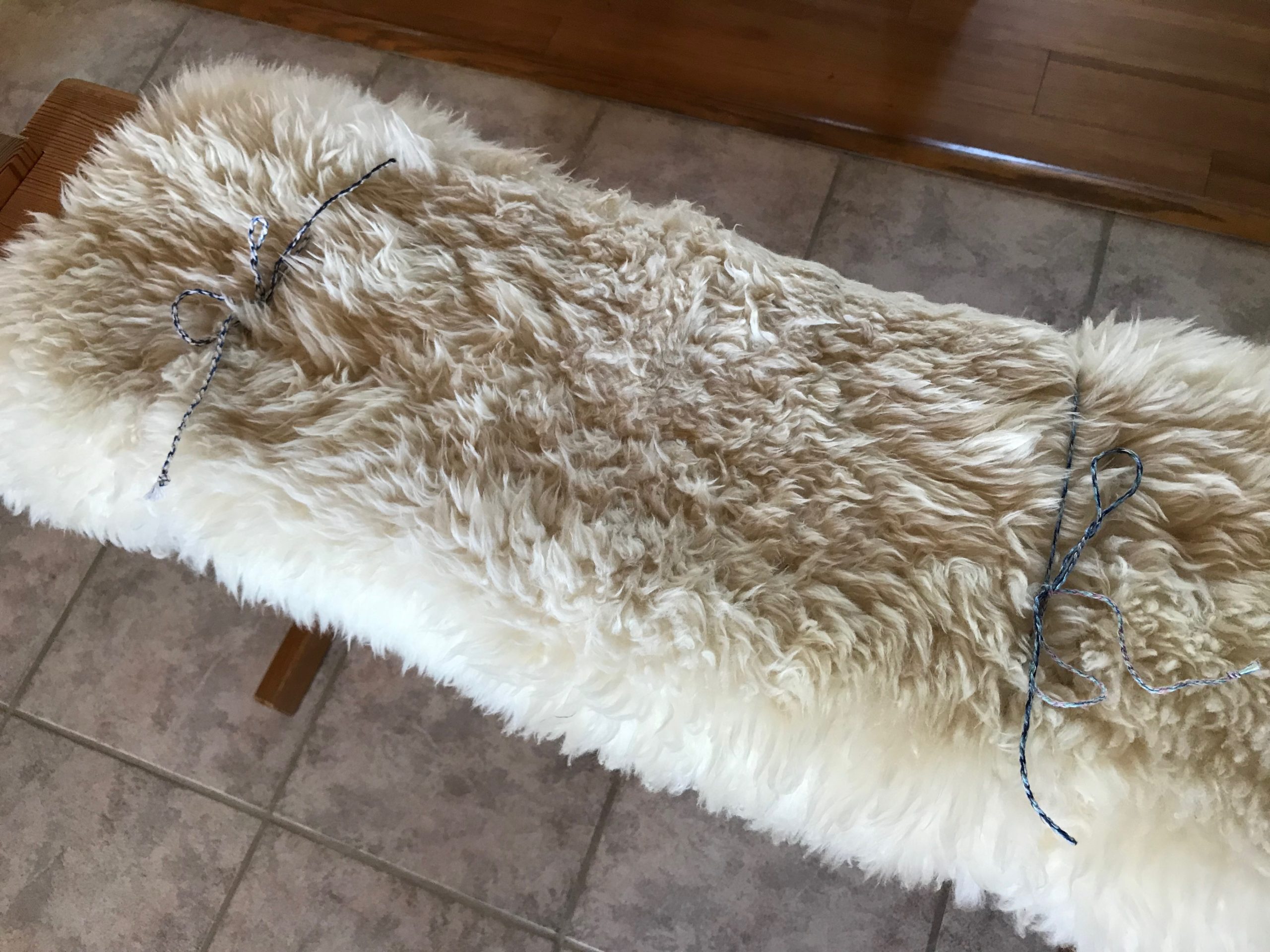
Make a Sheepskin Loom-Bench Cover
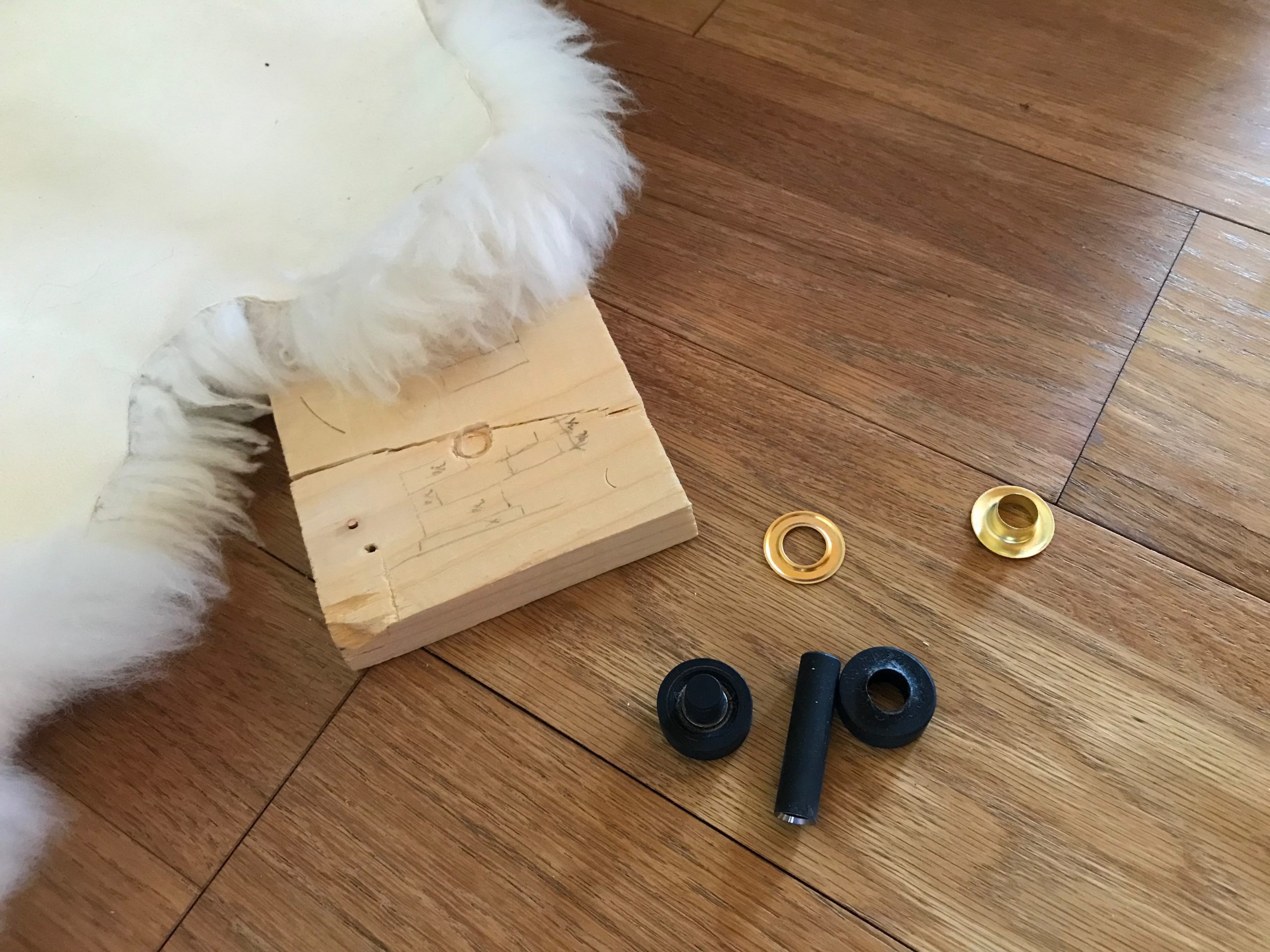
Supplies
- Sheepskin
- 6 3/8” grommets
- Pencil
- Grommet kit (hole punch, base, and flaring tool)
- Small block of wood
- Hammer
- Tape measure
- Texsolv cord (scissors, and small flame to sear ends)
- 6 Arrow pegs
1 Mark placement for 6 grommets on the underside of the sheepskin.
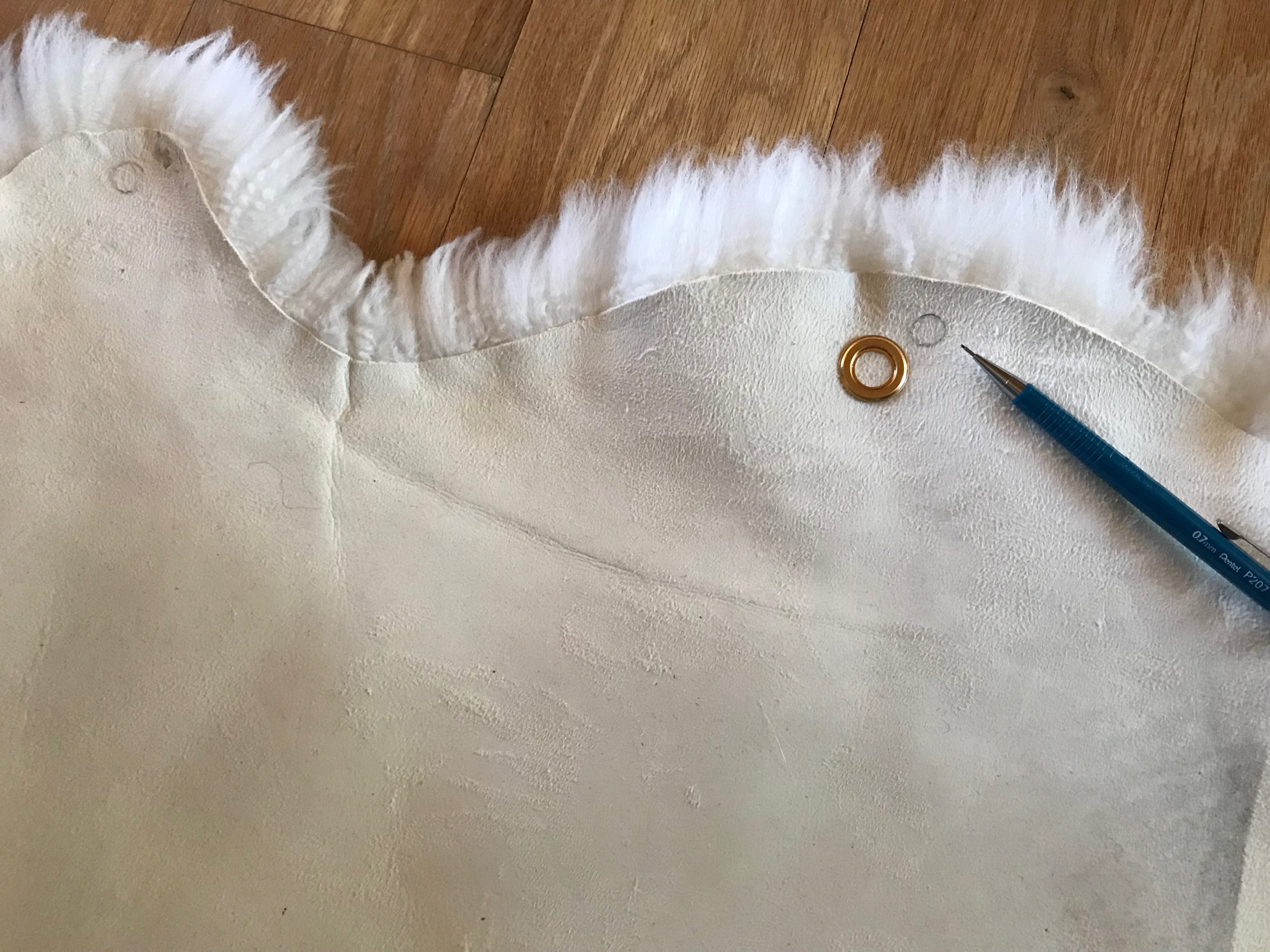
2 With block of wood underneath, hold grommet hole punch over one of the marked positions. Tap tool with the hammer to cut a small hole.
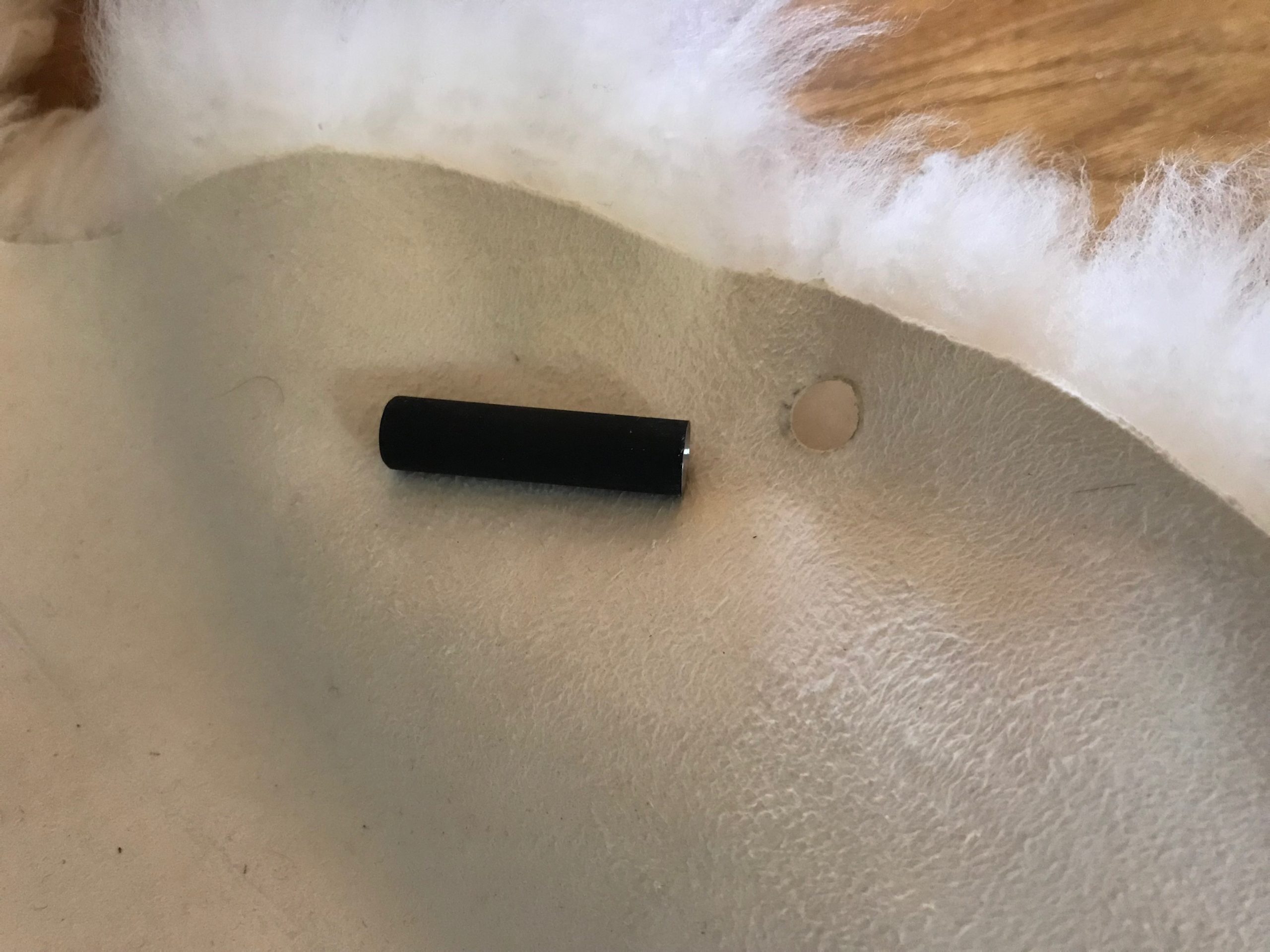
3 Insert the protruding ring of the top grommet piece (grommet) into the fur side of the hole.
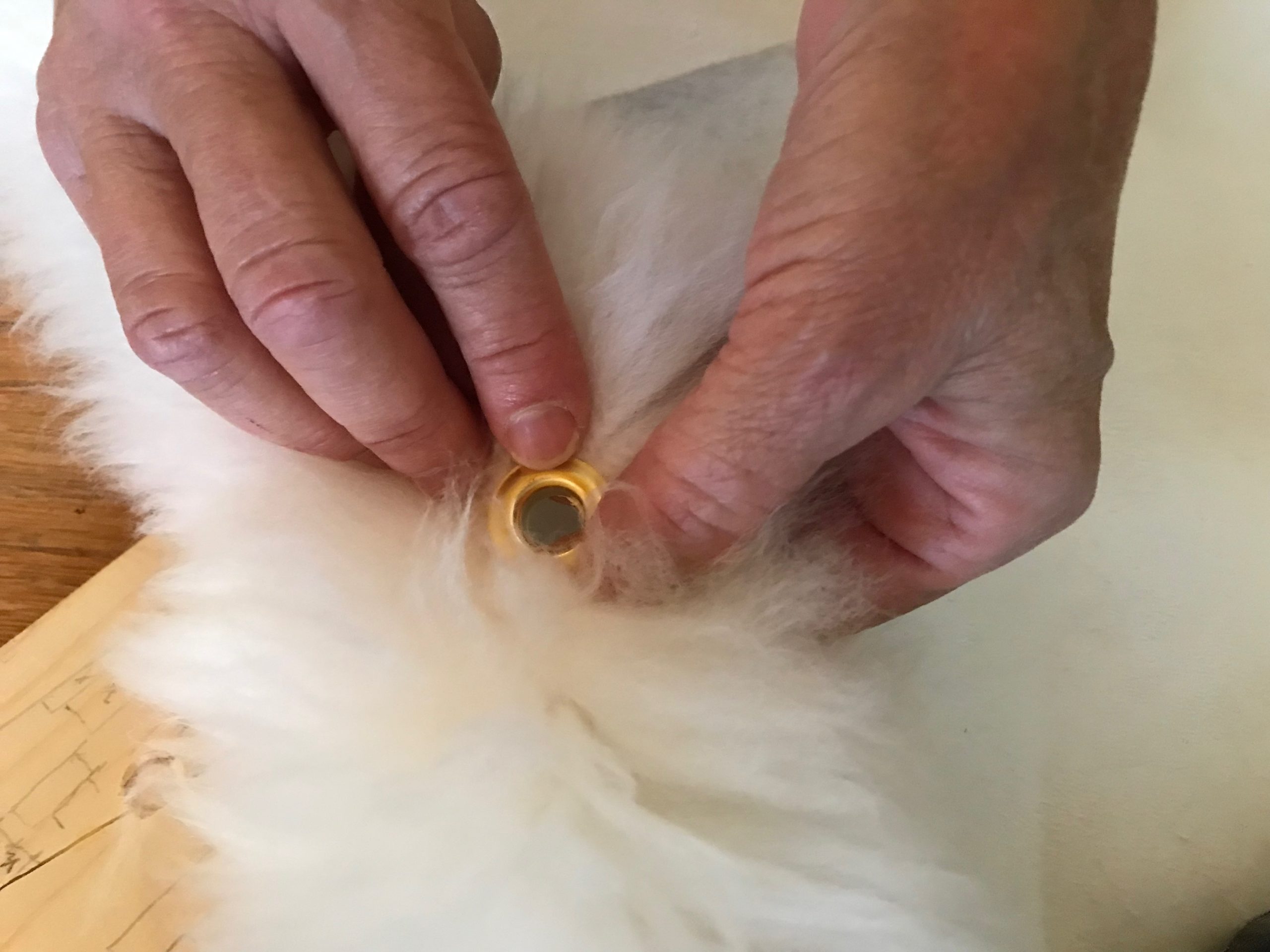
4 With fur side down on the block of wood, fit bottom grommet piece (washer) on top. Align grommet and washer between the base and flaring tool. Firmly tap with hammer until the two grommet pieces are tightly fastened together.
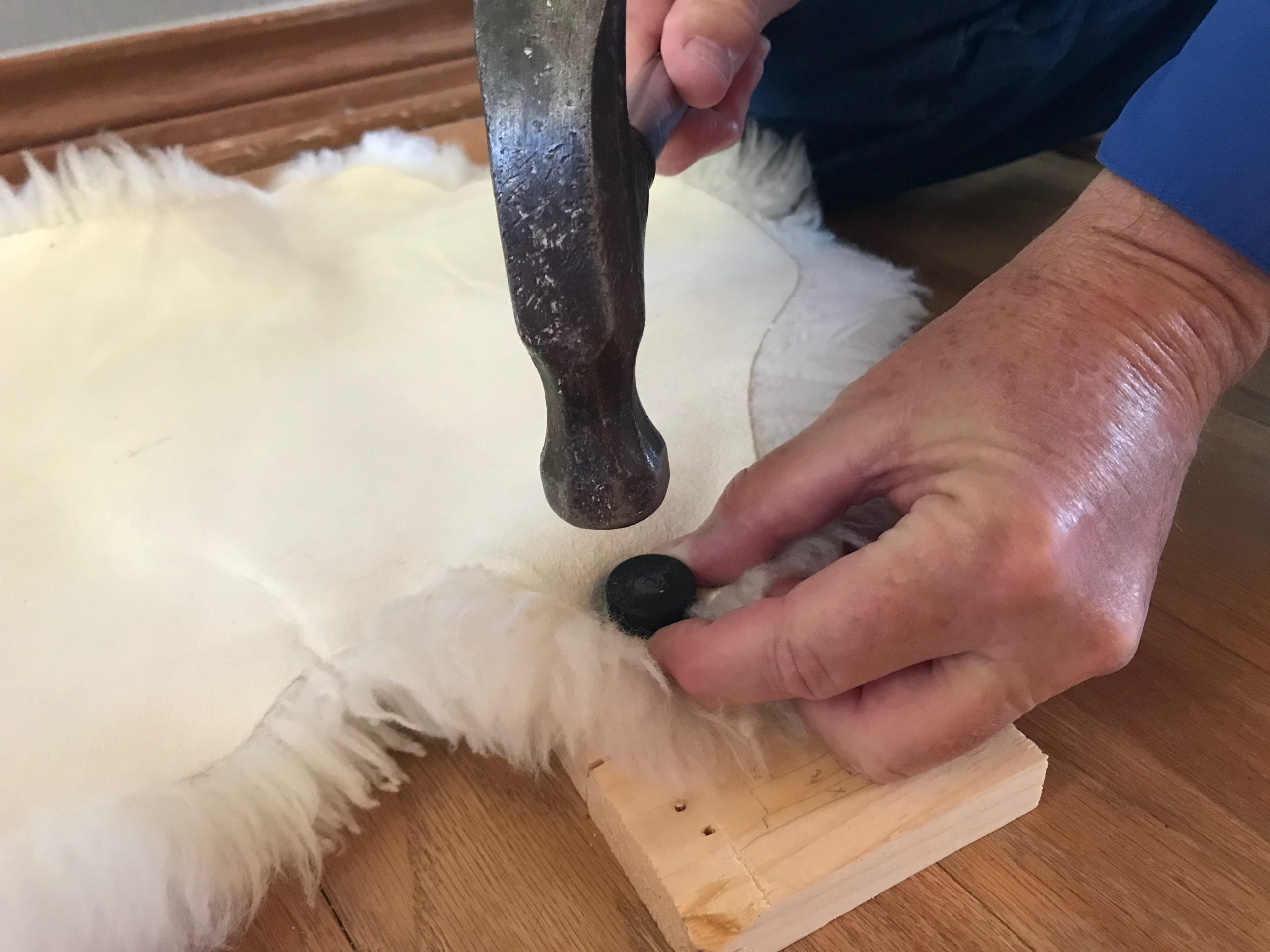
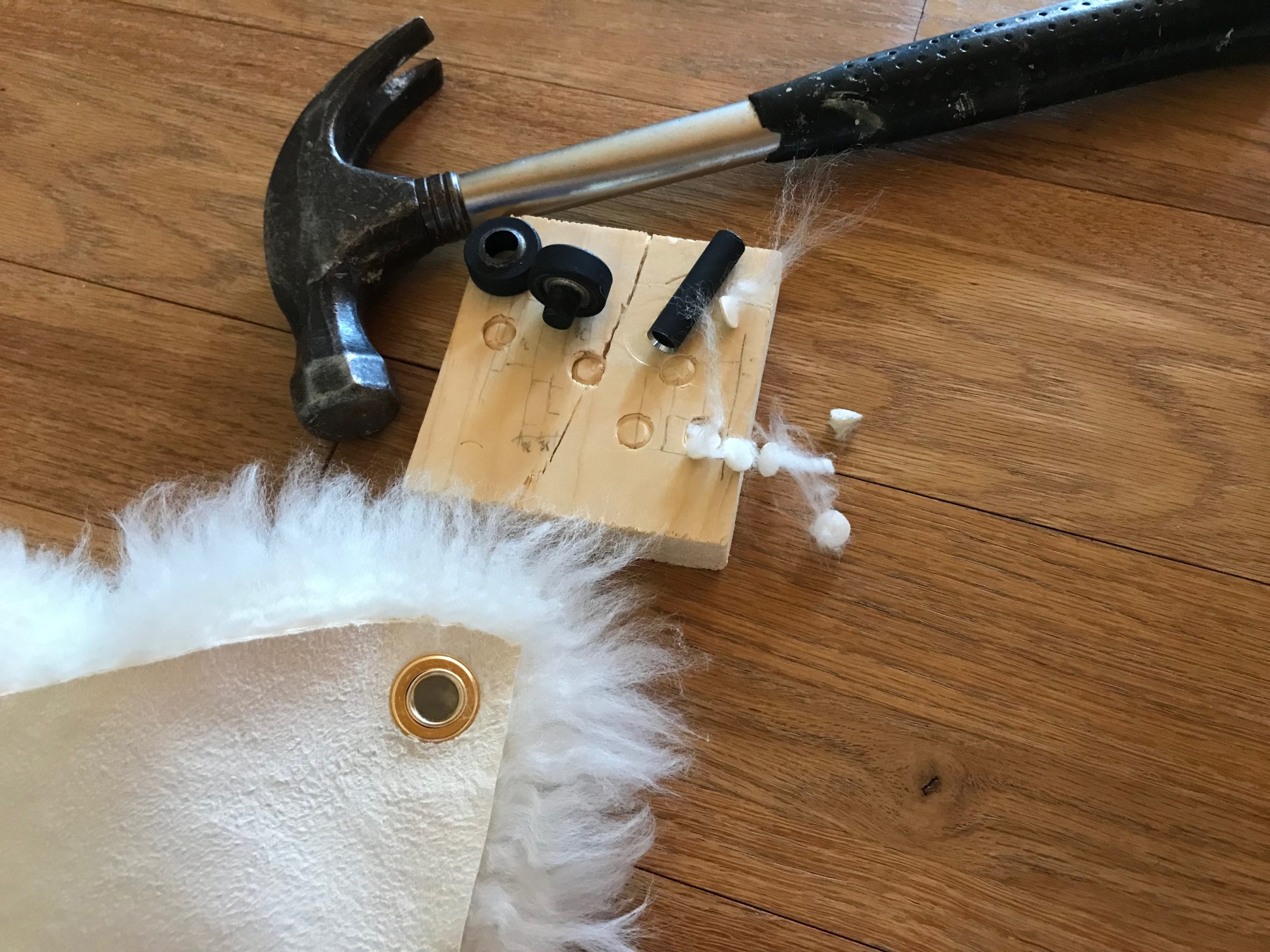
5 Repeat steps 2 – 4 for each of the 5 remaining grommets.
6 Lay the sheepskin fur-side down on a table or floor. Center the seat of the bench upside down on the sheepskin. Bring the sides of the sheepskin over the bench. Measure the distance between opposing grommets.
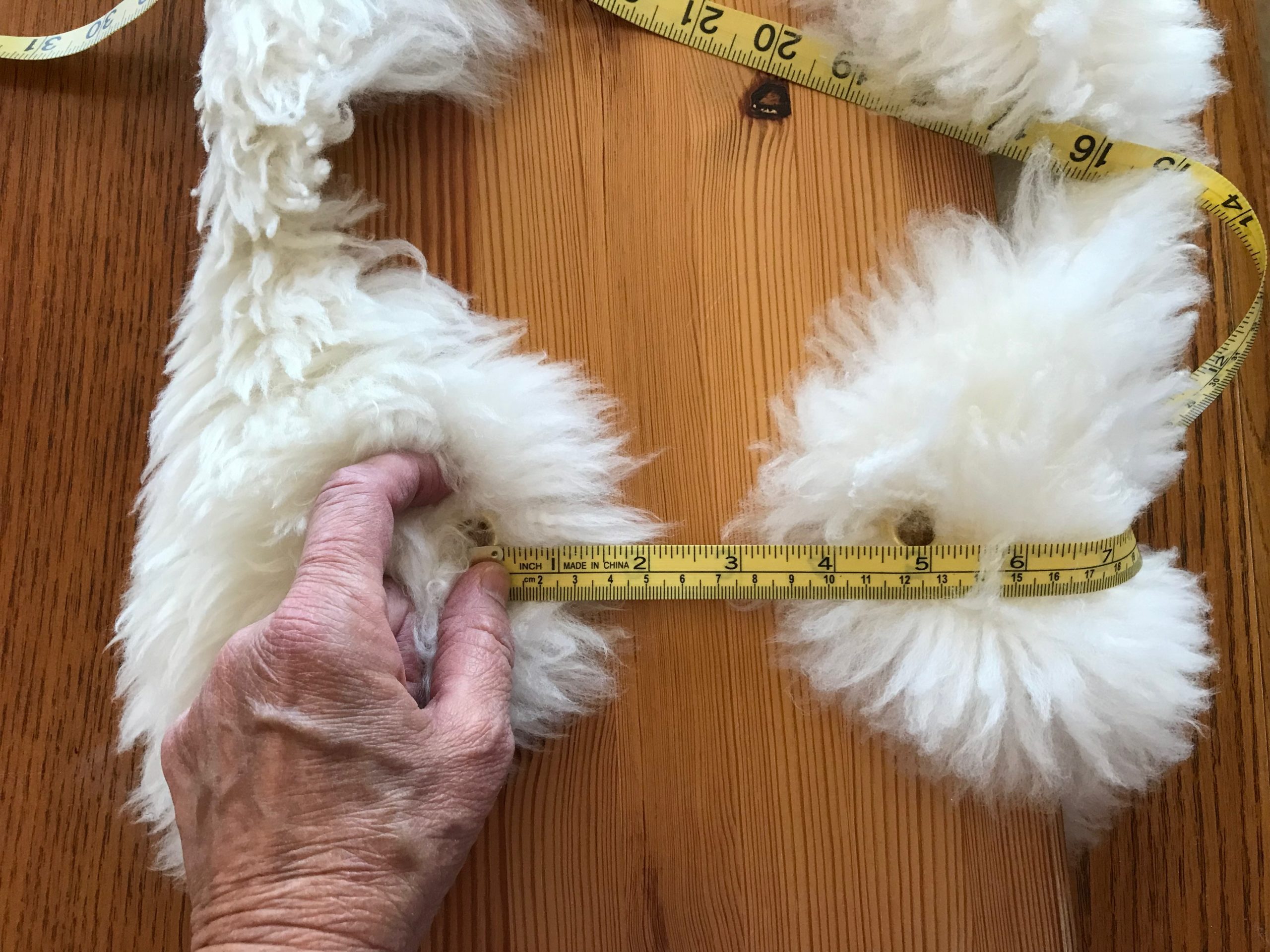
7 Double the grommet-to-grommet measurement, and cut three Texsolv cords that length. Sear the cut ends in a flame.
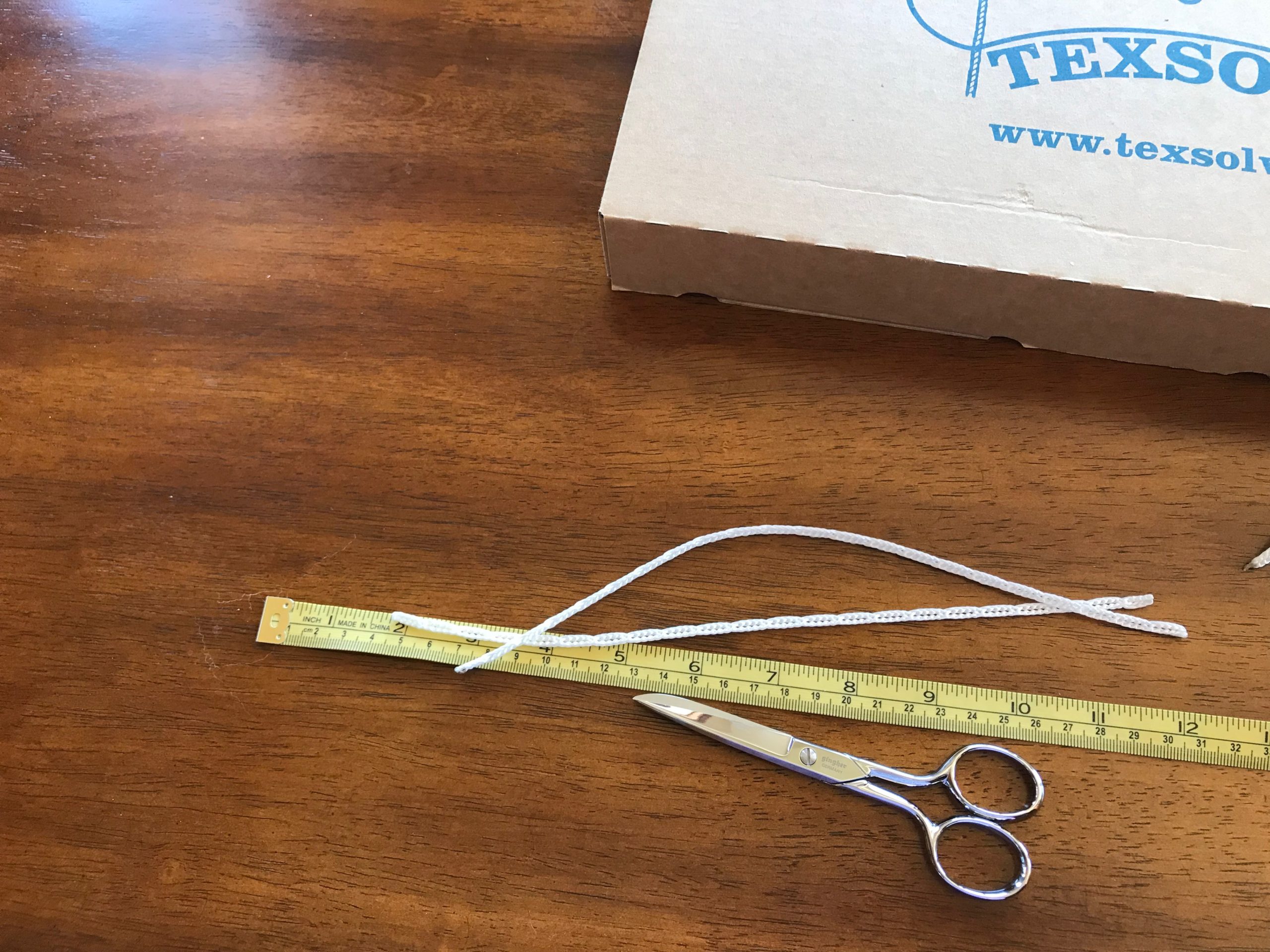
8 Secure the sheepskin to the seat of the bench by lacing one of the cut Texsolv cords through two opposite grommets. Tighten the cord and lock it in place with an arrow peg. Repeat for the remaining two cords.
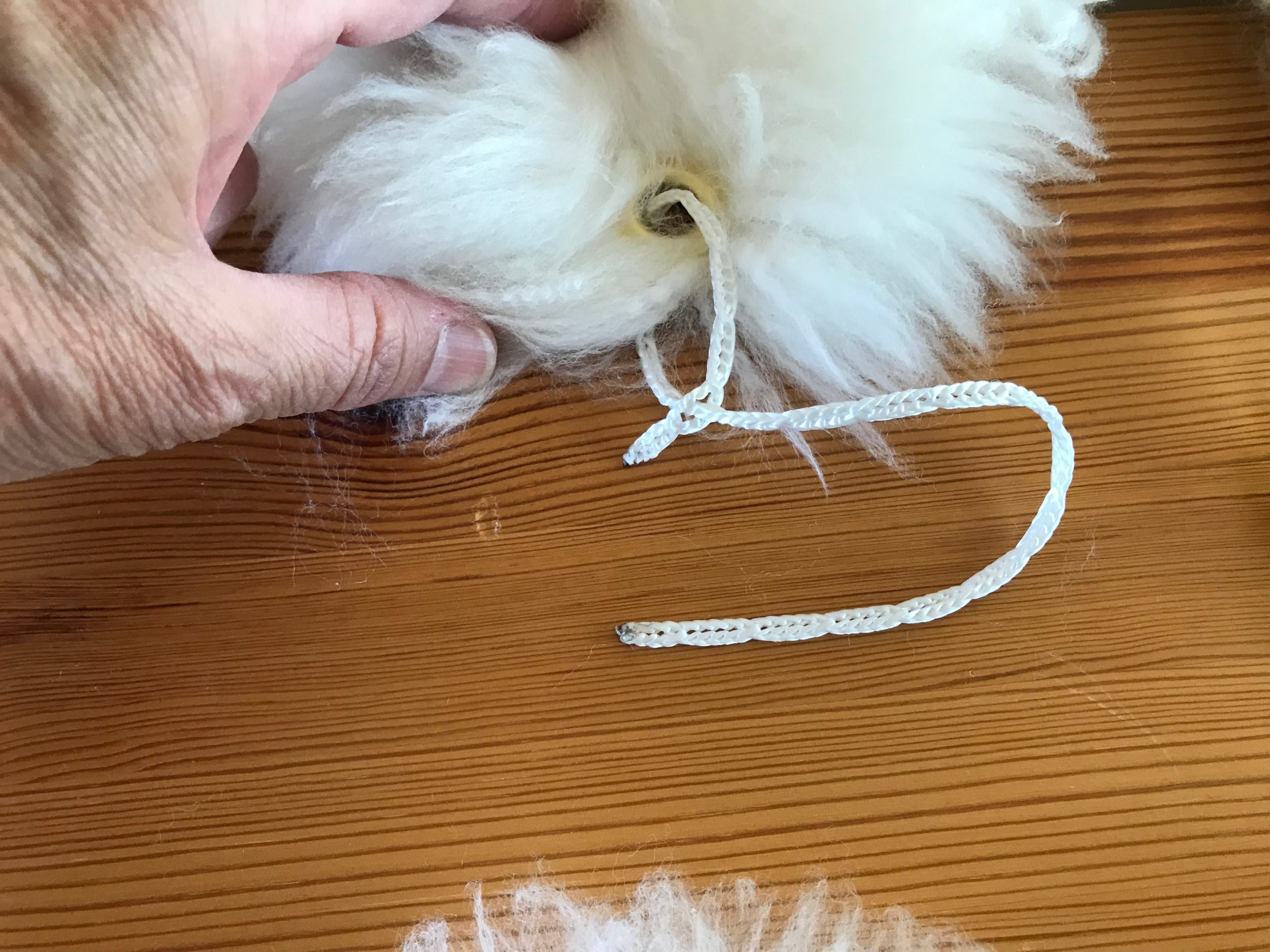
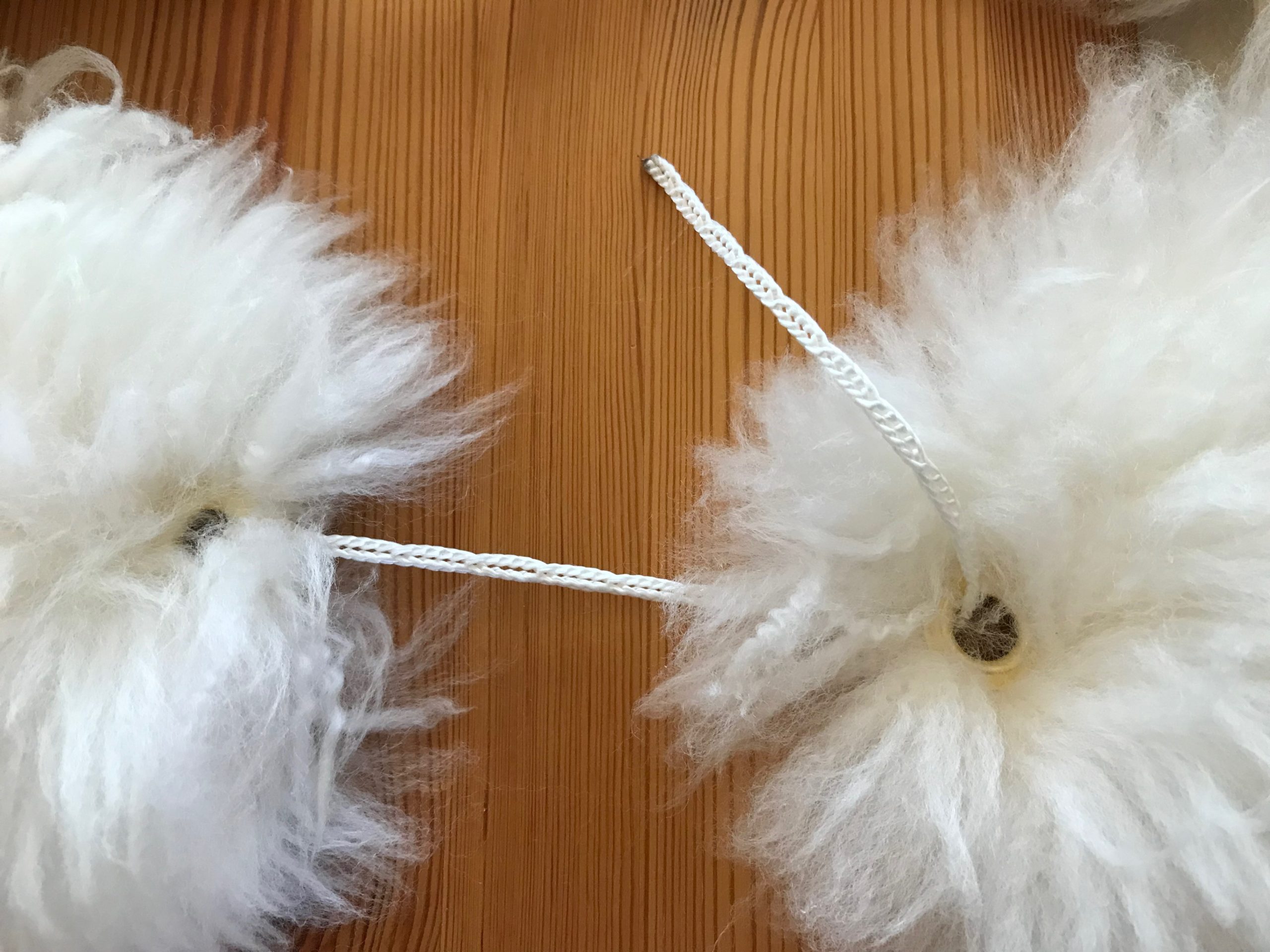
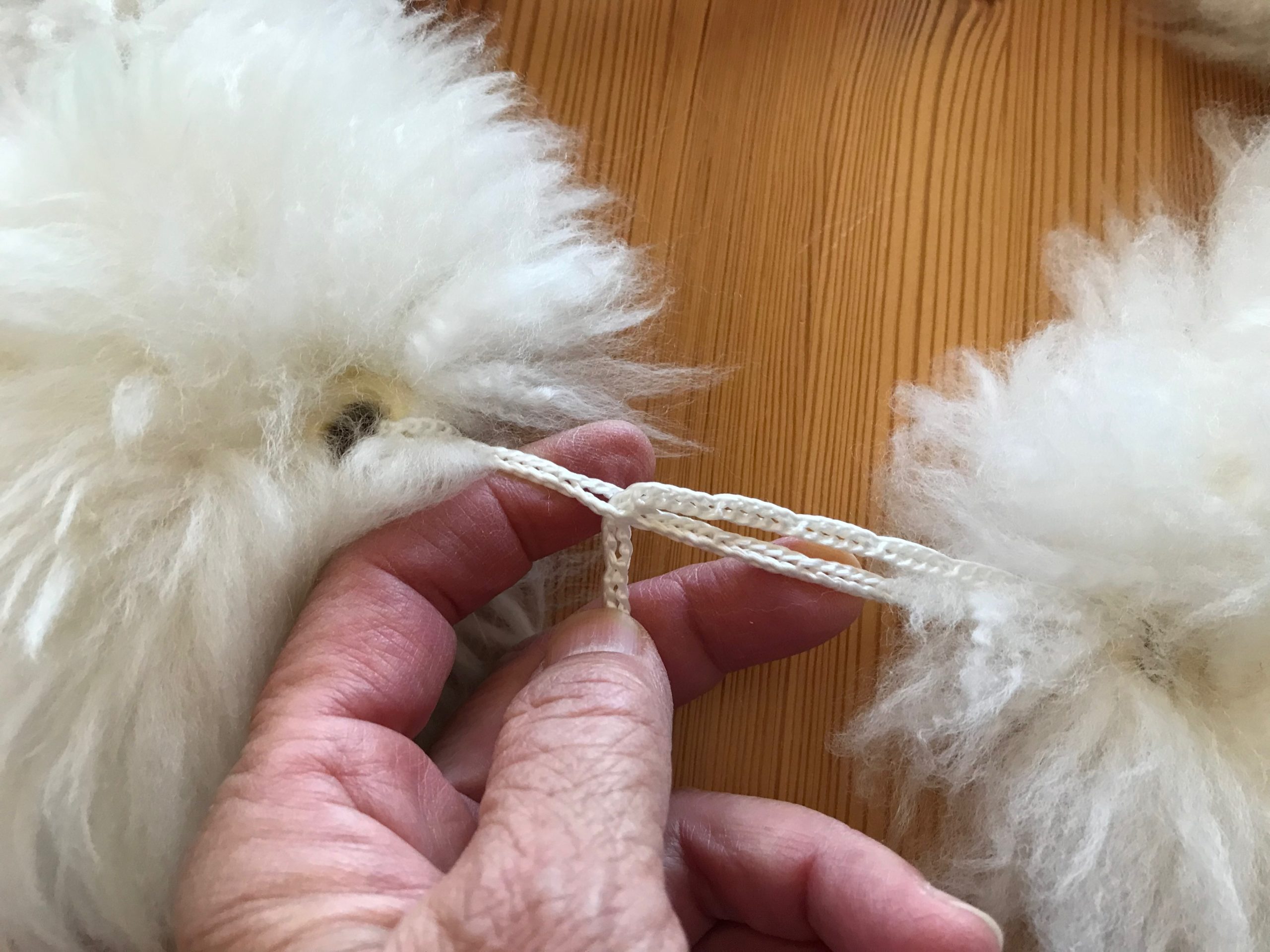
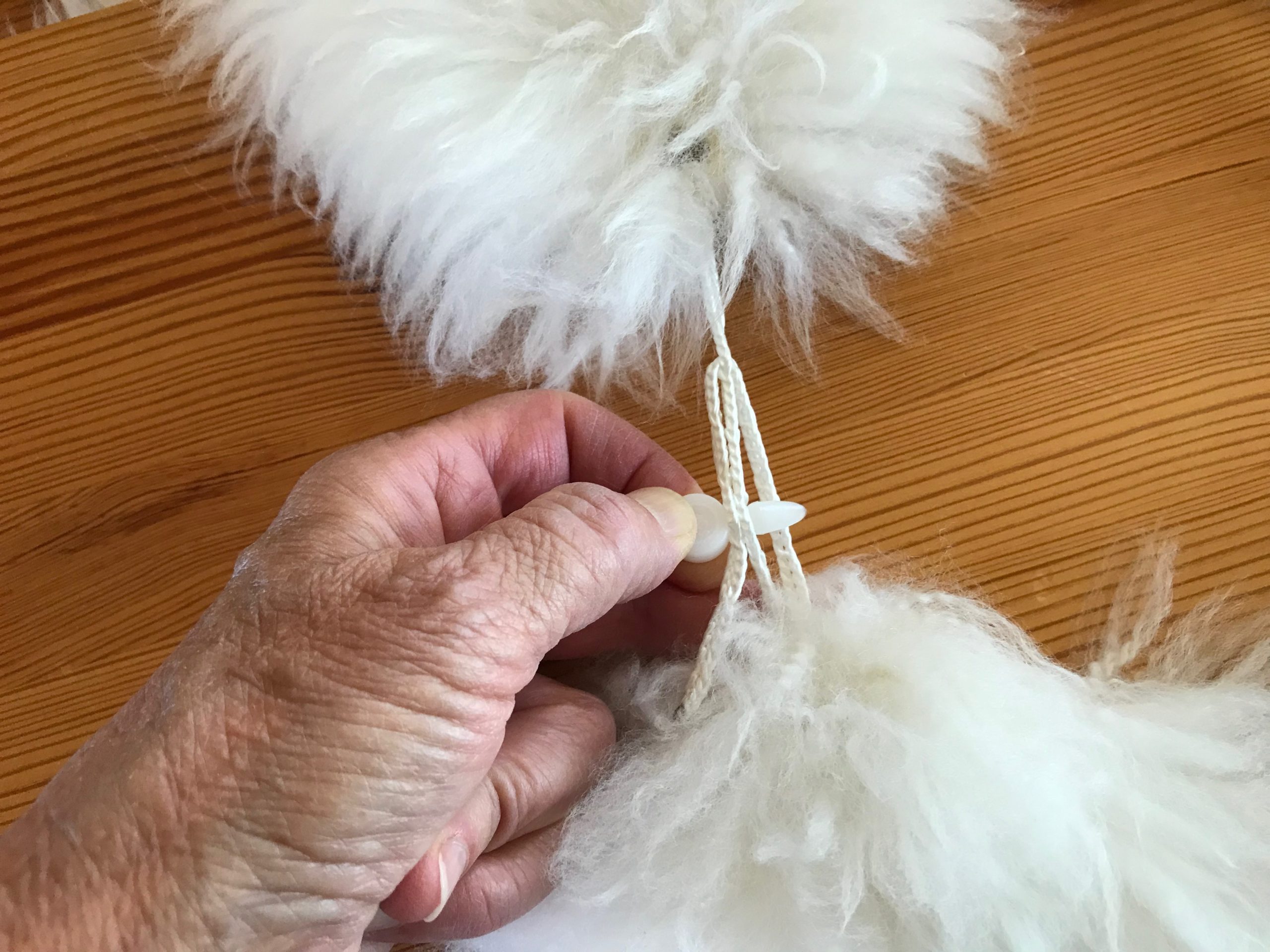
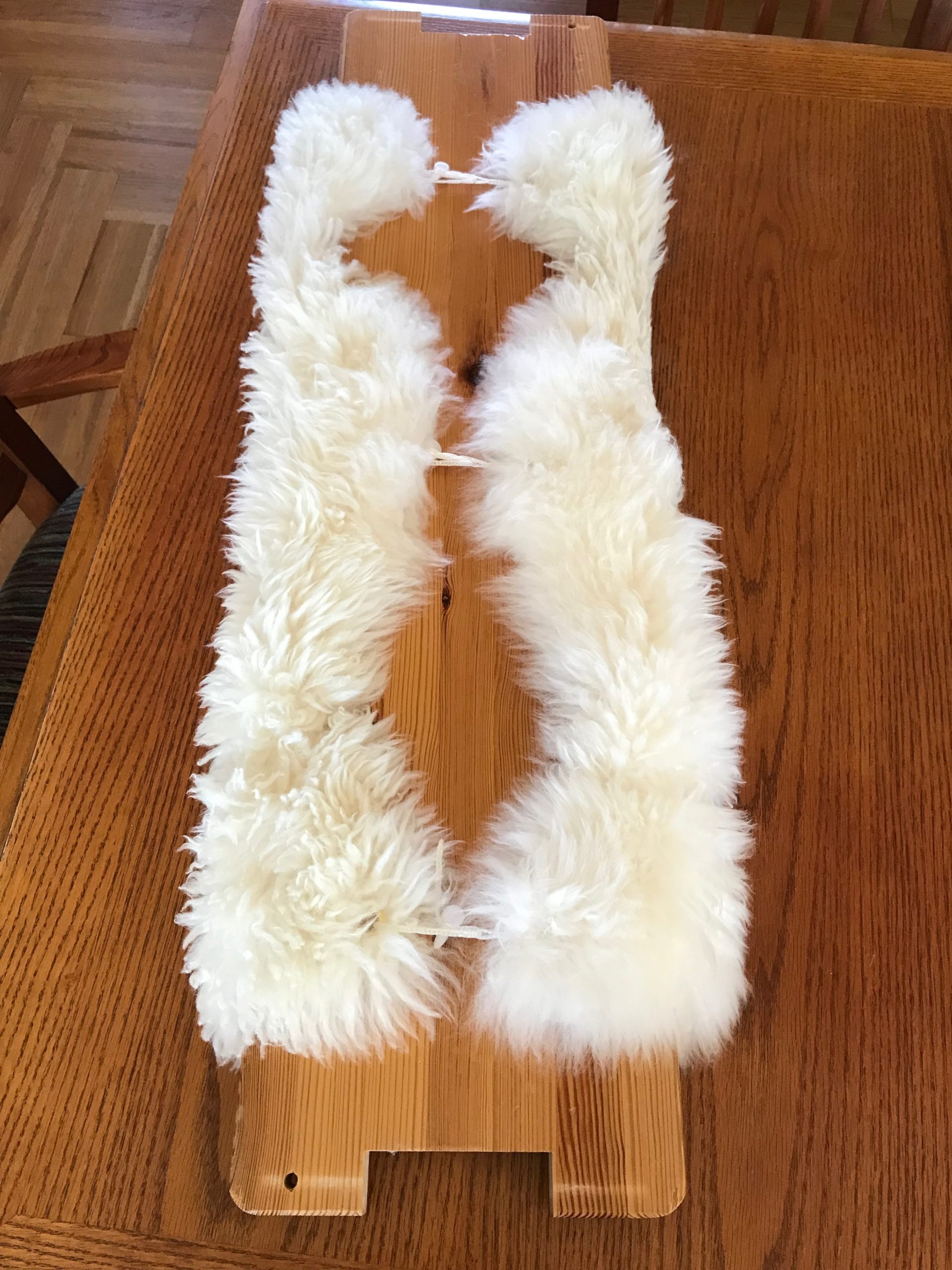
Sit in immovable comfort.
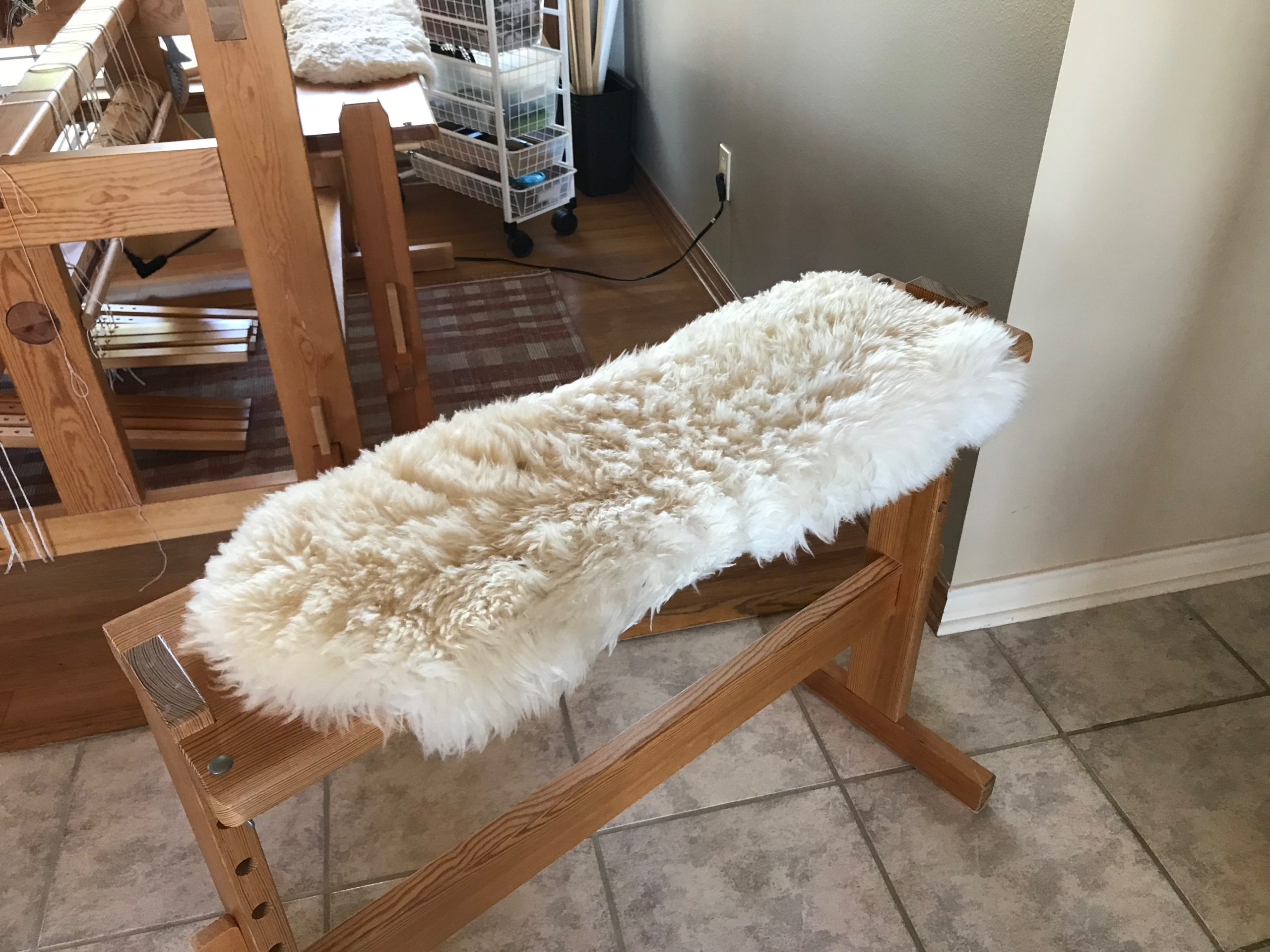
While we’re at it, let’s fix up one more bench cover…
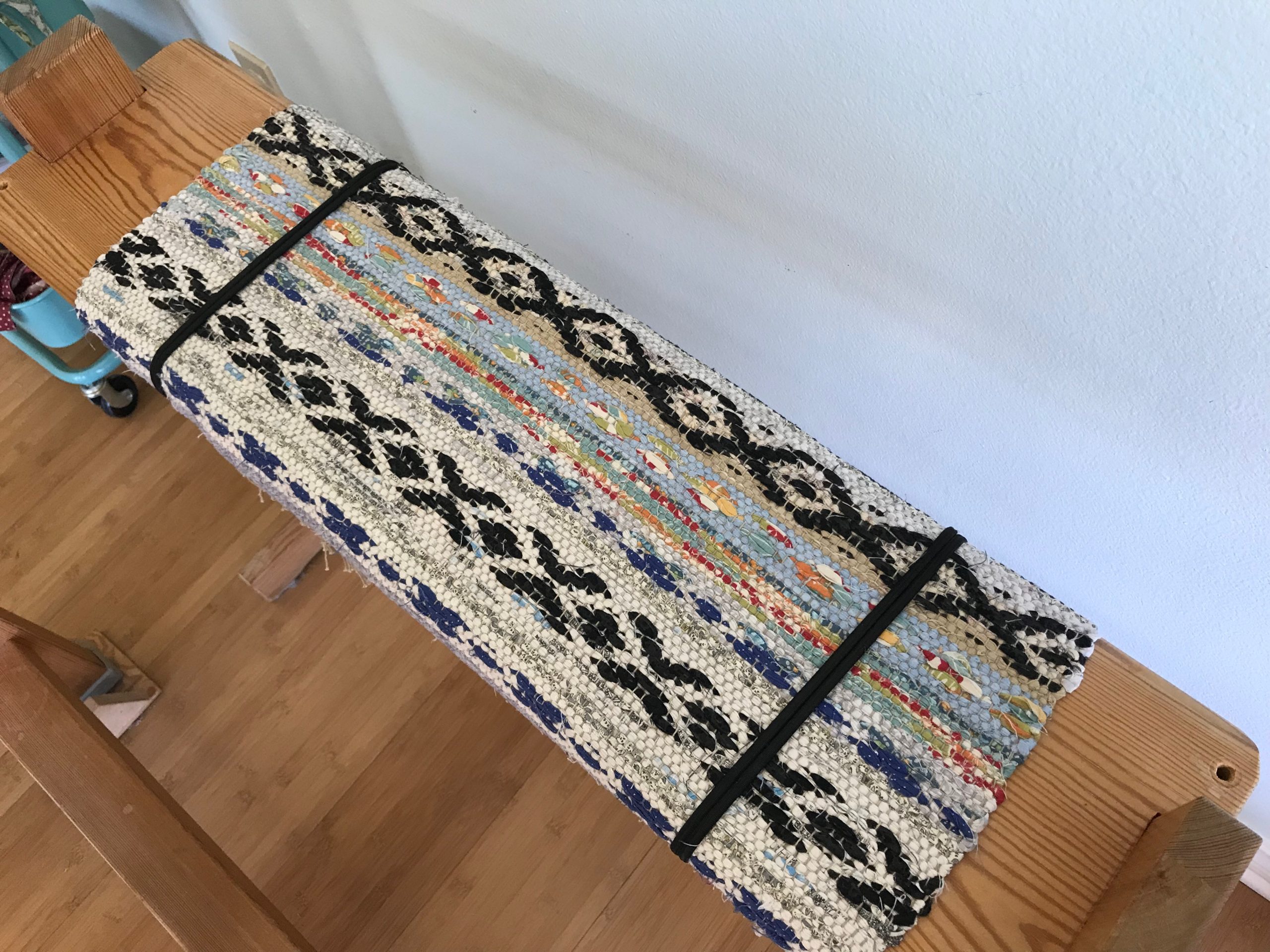
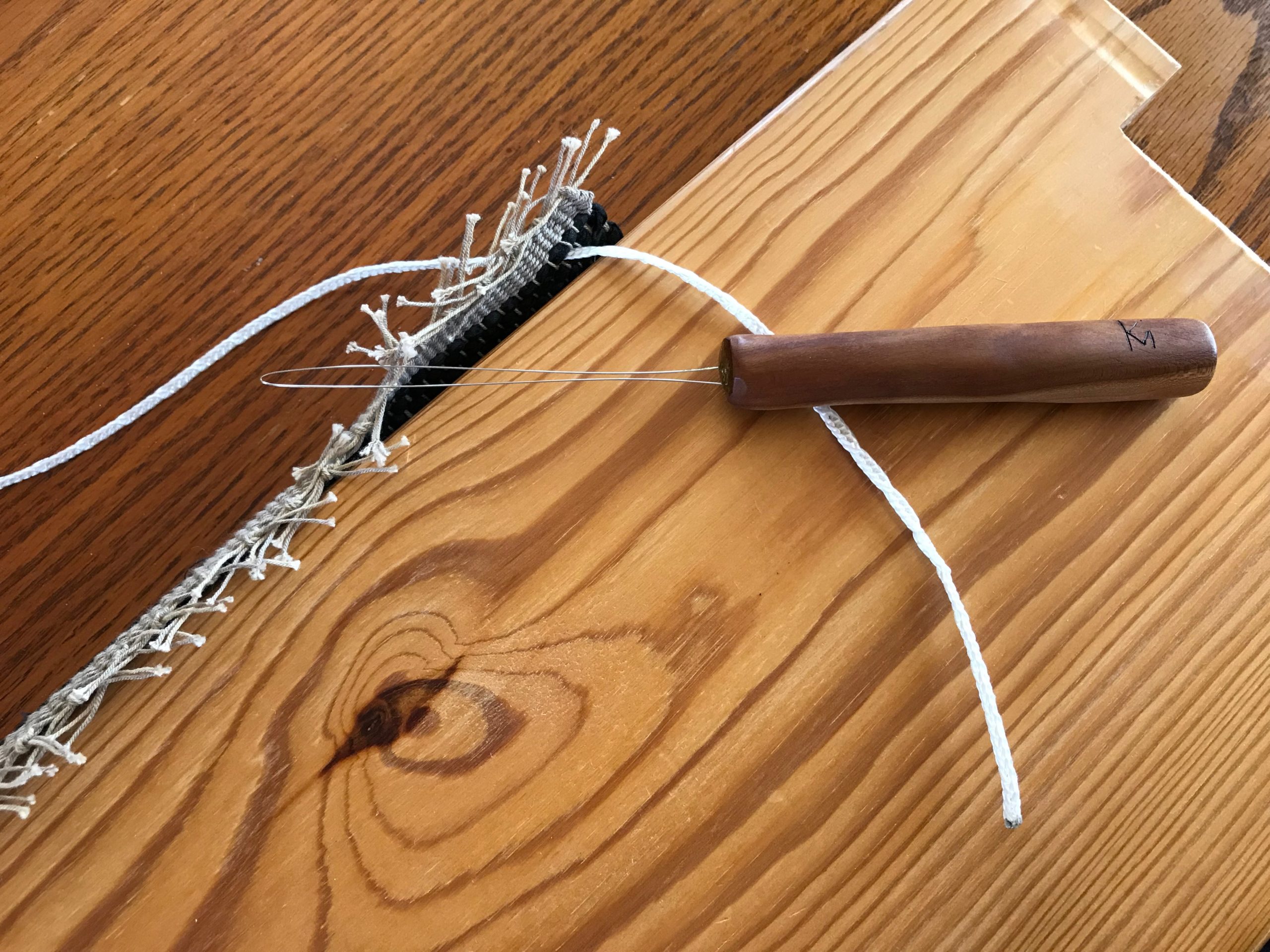
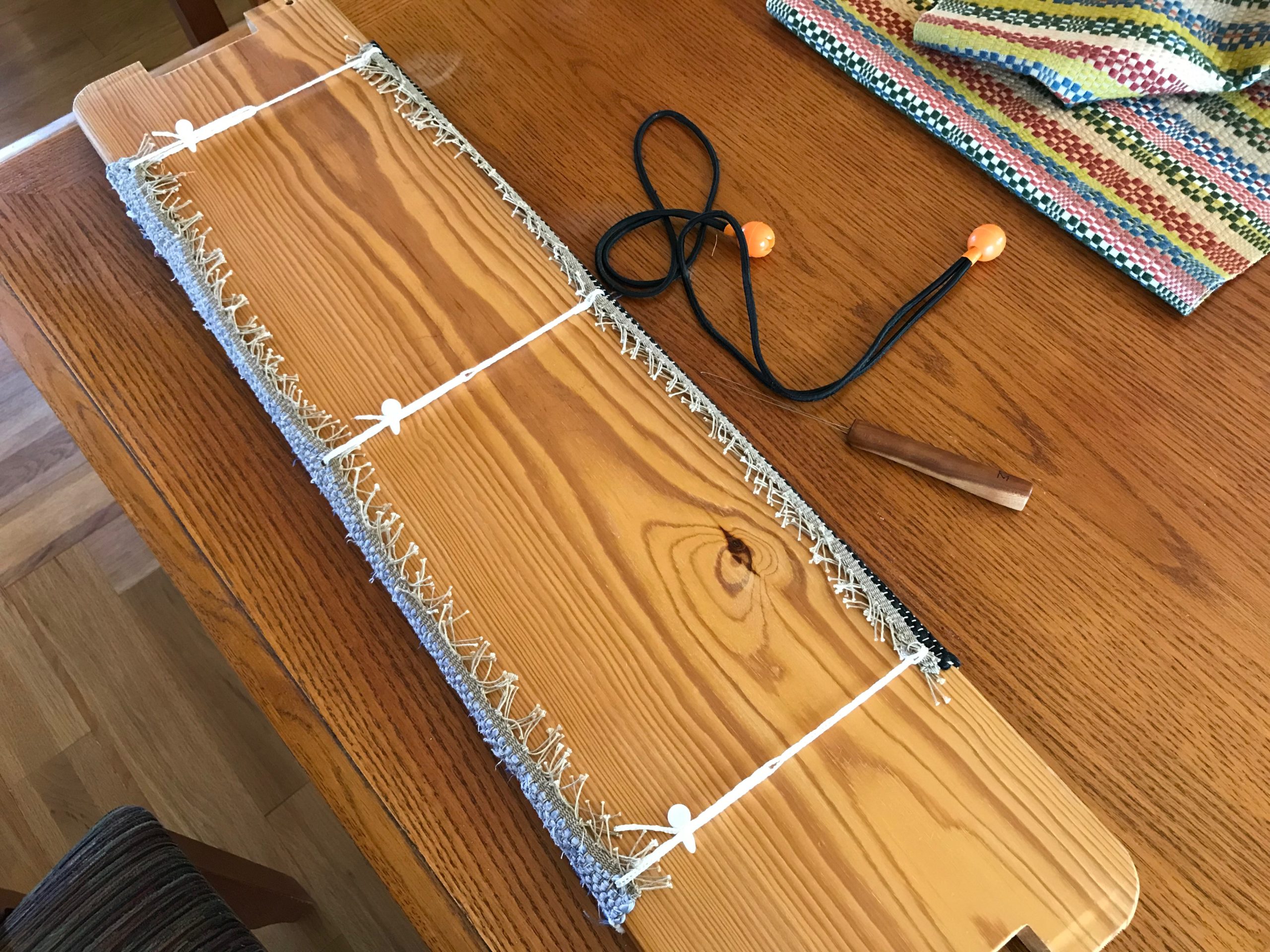
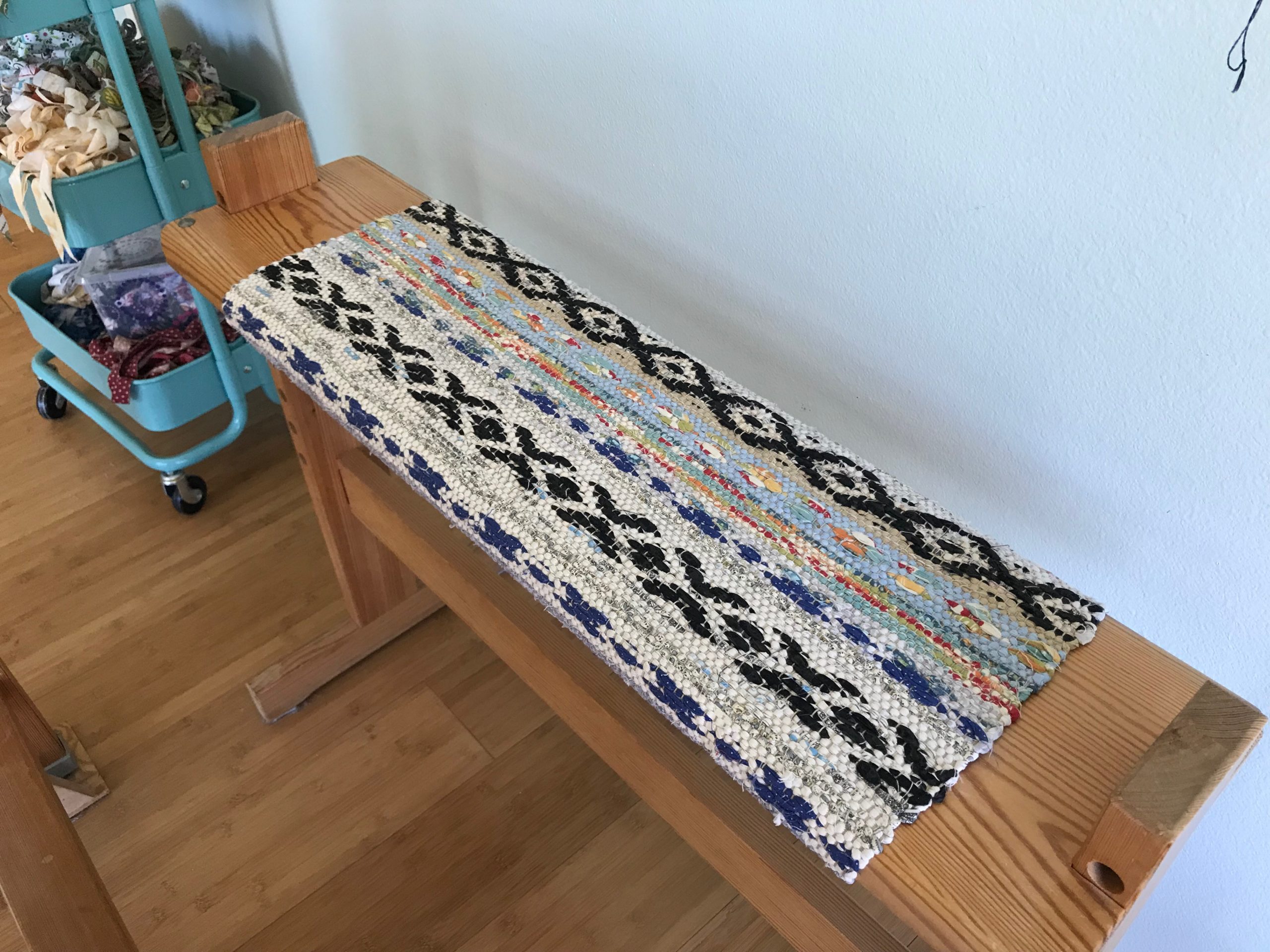
May you see where you can soften things up.
Happy Sitting,
Karen